コラム
どんなに手間暇かかっても徹底して美しさを求める
2021.06.11
STORY9
樋渡が学生だった頃、工作で何かを作り始めると、あれもして、これもしてとどんどんクオリティを上げていこうとして、しまいには提出期限に間に合わなくなることが多々あったという。
このものづくりの妥協のなさが、アールズ・ギアの製品にもしっかり根付いている。
樋渡のマフラーつくりにおけるポリシーは、自分がそのマフラーを付けたとして、性能アップはもちろんのことで、そのうえで見た目の美しさにも十分満足できるかどうかということ。マフラーを筆頭に、バイク用パーツは基本的に外から見えるものだから、徹底的に美しく仕上げるのが樋渡のやり方だ。
そのこだわりはひとつひとつのパーツに込められていて、サイレンサーを車体と結ぶステーひとつとっても形状、仕上げとも一切手を抜くことはない。集合部は絶対にプレス材を使用せず、パイプを溶接して組み上げる。4in1集合の場合は、集合部にピラミッド構造を採用し、見た目は4in1でも集合部にセパレーターを入れて4in2in1構造にするなど、性能向上のためにできることはすべて行っている。
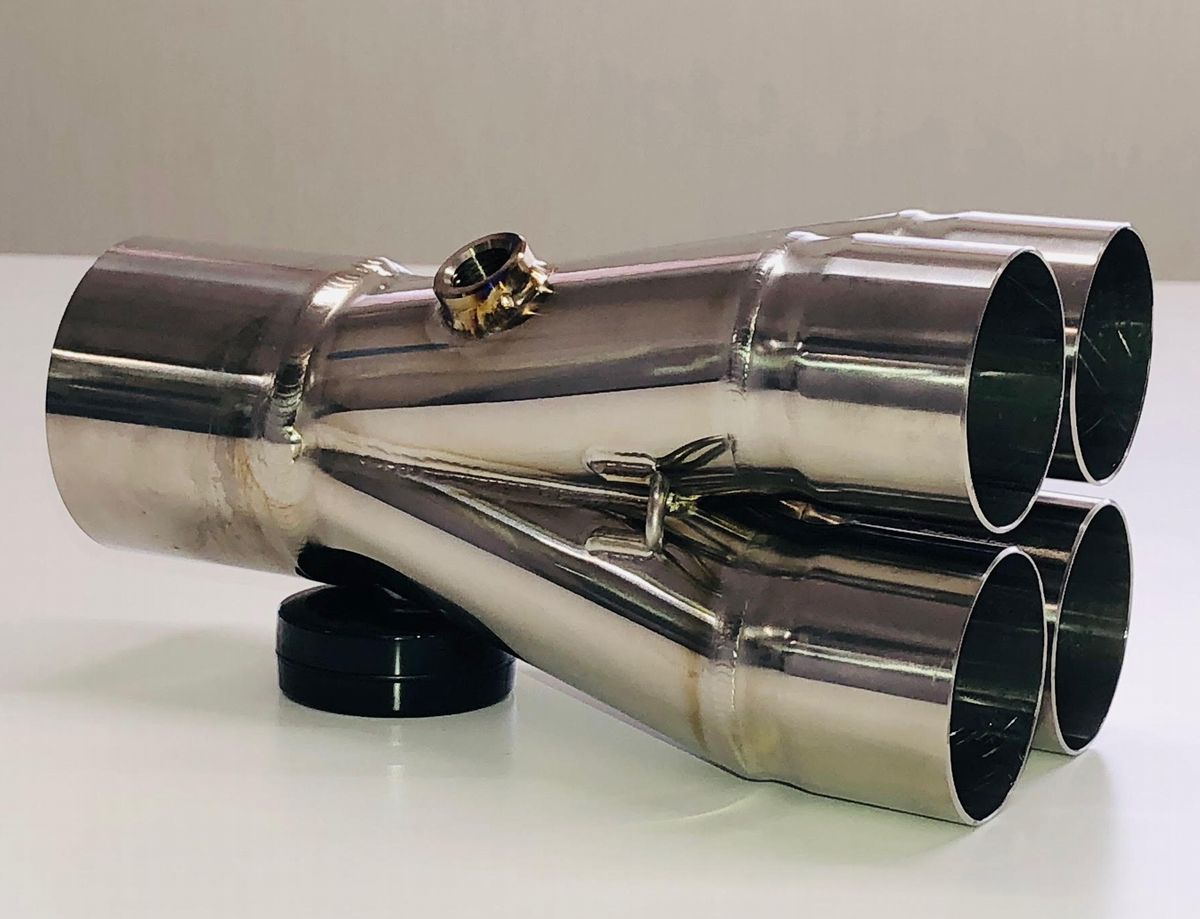
↑集合部もプレス材は一切使わず、パイプを切って曲げて溶接して組み上げる。写真の4in1タイプは集合部にセパレーターを入れて、実質4in2in1構造としている。すべては性能向上のためだ
樋渡がここをもっとこうしようと言うと、スタッフにそんなことしてもちょっとしか変わらないから無駄ですよと言われることもあるそうだが、少しでも良くなるならどんなに手間がかかってもあえてやるのが樋渡流だ。
機械曲げのチタンパイプも徹底的に表面処理を行って、バーナーであぶってきれいな焼け色を付ける。マフラーは性能アップのための機能部品だがバイクの場合はドレスアップパーツでもある。だからこそ、エキゾーストパイプの取り回しの美しさやきれいな焼け色、サイレンサーの取付け角度など、常に美しさを意識して開発作業を行っている。
機械曲げを行う際も、エキゾーストパイプが手曲げに近いアールを描くように、曲がる角度の違う型をいくつか使用して丁寧に作り込んでいる。できることは可能な限り行うのがアールズ・ギアのものつくりなのだ。
そして、溶接部の美しさもアールズ・ギアのマフラーの大きな特徴だ。パーツ同士を接合している部分はすべて溶接で行っていて、一番溶接箇所が少ないという4気筒の4in1モデルでさえ、パイプ部分だけで10カ所、集合部分は18カ所、サイレンサーはものにもよるが少なくても10カ所、多ければ12カ所にものぼるという。
溶接作業は現在、5人のスタッフで行っているが、丁寧に時間をかけて行っているがゆえに、なかなかオーダーをさばききれない状態が続いているという。もちろん、溶接箇所を減らす作り方もあるにはあるが、アールズ・ギアではあえて手間のかかるつくり方を選んでいる。
ライダーがライダーのために作るマフラー
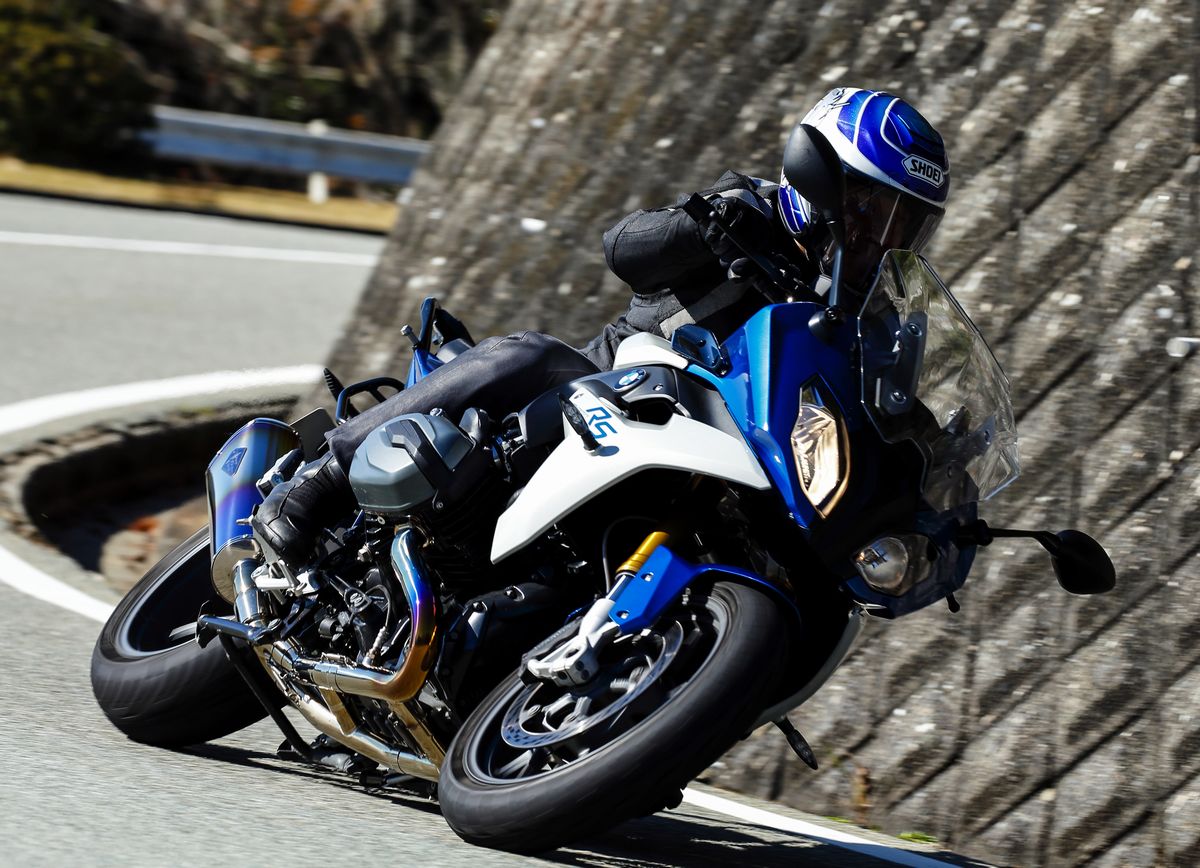
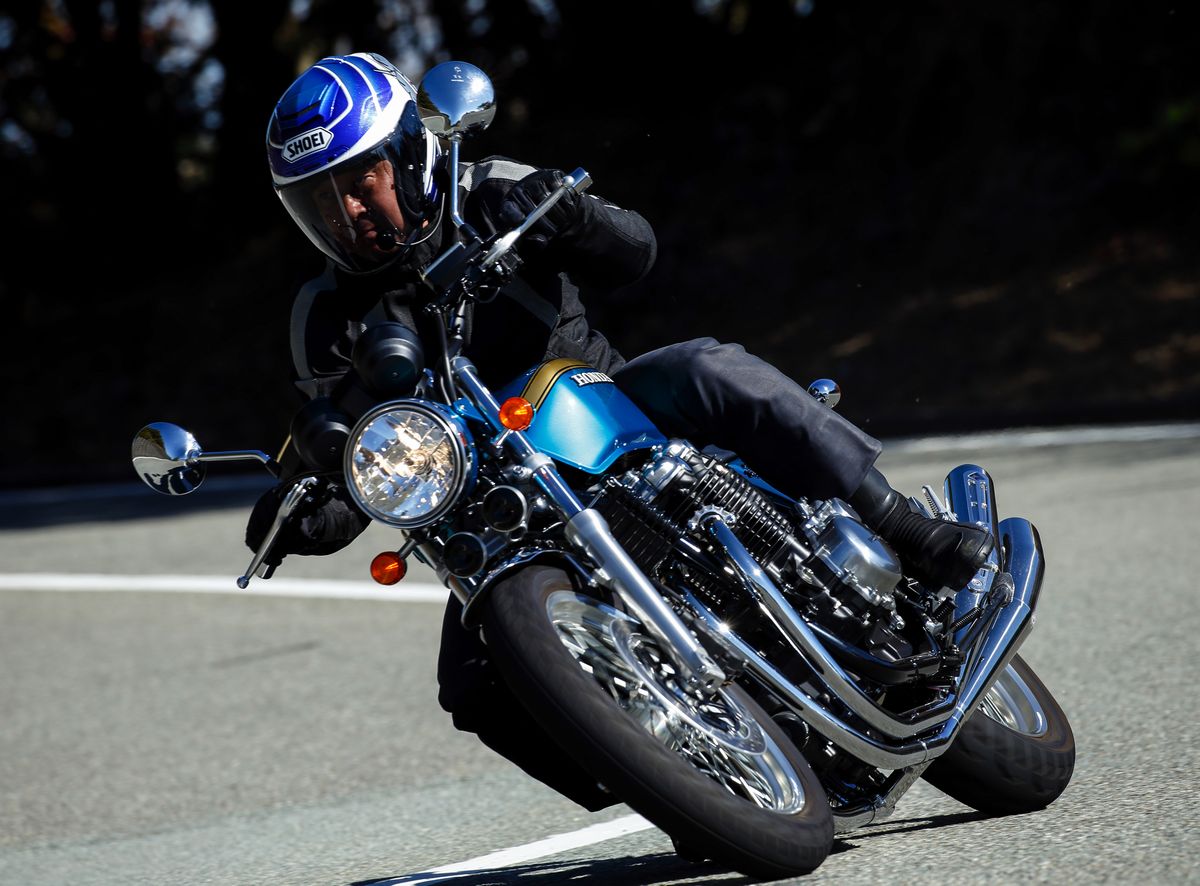
↑開発に当たっては、樋渡自身が徹底的に走り込んで性能を突き詰めていく。単にパワーとトルクが出ているだけではなく、スムーズで扱いやすく、長時間乗っても疲れない特性を作り上げていくのだ
この理由は、樋渡自身がライダー出身だからだと言う。ライダーだから、自分のバイクはとことんカッコよさにこだわりたい。性能はもちろんのこと、付けたときの満足感も重要なポイントだと考えている。
意外な感じだが、代表がライダー出身のマフラーメーカーというのはほとんどなくて、いまある多くのマフラーメーカーの代表はメカニック出身者がほとんど。アールズ・ギアでも、メカニック出身の設計スタッフが見た目のカッコ良さよりも性能重視で製作しようとすることがあるという。メカニックという職業柄、彼らは性能さえしっかり出ていればそれでOKと考えがちだが、樋渡は絶対に納得せず、あくまでも性能と美しさの両方を求めるのだ。まさにライダー目線のライダーのためのマフラーなのだ。
この徹底的なこだわりのせいで、開発から発売まで2年半も要したモデルがある。それはCB1100の4本出しマフラー(ワイバンクラシック 4本出し ステンポリッシュ)で、どうしても往年のCB750Fourの雰囲気を忠実に再現したかったのだが、写真を何度見てもどうしてもカッコよくならなかった。排気音も、自分の記憶にあるものとは異なっていた。
結局、レストアしたCB750Fourを購入し、それをCB1100の横において開発をはじめたらやっと納得できるものが出来上がった。お客さんからも、まさにCB750Fourだねと言ってもらえるような仕上がりで、発売後もコンスタントに売れているという。
(STORY10に続く)